Mechanical pressure gauges, which require no external power, provide an affordable and reliable source of accurate pressure measurement. The need to select the right pressure gauge requires that the device be accurately specified otherwise numerous problems might surface in the course of using a wrongly selected gauge.
Pressure Gauge Selection
The factors discussed here are by no means exhaustive but they are the main things that will assist you to select the right type of pressure gauge. For the right specification and selection process, consult the manufacturer of the particular gauge you intend to use.
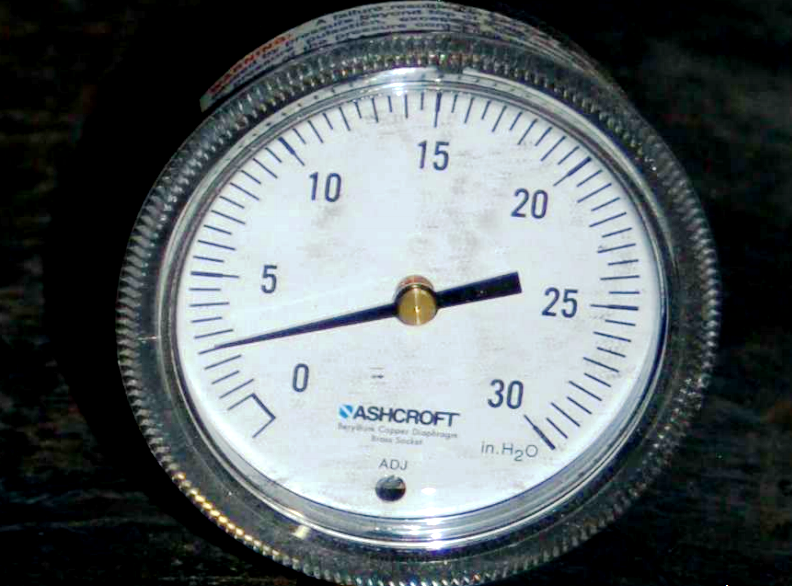
Pressure gauges should be selected by considering the factors below to prevent misapplication. Improper application can be detrimental to the gauge, causing failure and possible personal injury or property damage.
To select the right pressure gauge for your application, the following factors should be considered:
Gauge Accuracy
Pressure gauge accuracy ranges from grade 4A to D according to ASME 40.1. For a mechanical pressure gauge, accuracy is defined either as a percentage of the full-scale range or a percent of the span. As the accuracy increases, so does the price of the gauge.
Therefore, the application where the gauge is required should be carefully considered before deciding on the accuracy of the gauge.
While requirements differ from one industry to another, the following are general guidelines:
- Test Gauges and Standards: 0.25% through 0.10% full scale accuracy.
- Critical Processes: 0.5% full scale accuracy.
- General Industrial Processes: 1.0% accuracy. Less Critical Commercial Uses: 2.0% accuracy.
Gauge Dial
The dials of pressure gauges come in various sizes. They range from “1.5 to 16” diameters. Generally, the ease with which the gauge could be read, space limitations and accuracy requirements determines the dial size.
Larger dial size pressure gauges are required in areas of a plant that are not accessible while smaller sizes are may be required for areas that are easily accessible. The need for higher accuracy in an application may require that a pressure gauge of considerable dial size be used in a given location so as to enable the easy display of small pressure increments.
The Environment
Environmental factors to consider when selecting a pressure gauge include: ambient temperature, air-borne particulate, condensation, humidity, water and chemicals, all of which can affect gauge performance.
Ambient temperature affects the accuracy and integrity of the gauge. Gauges are available either as temperature compensated or non-temperature compensated. Ambient conditions may require that the gauge be isolated from temperature extremes. When required, the gauge should be isolated from temperature extremes with a flexible line assembly.
When ambient conditions are corrosive, contain a large number of particulate or if the gauge will be exposed to a wet or humid environment like humidity, wash-downs or rain, specify a gauge that is weatherproof/hermetically sealed or liquid filled.
Process Media/Wetted Parts
Proper selection of the pressure sensor material of the pressure gauge is dependent on the process fluid to which the gauge will be subjected.
The material of the pressure gauge sensor should be compatible with the process fluid such that corrosion will not occur. If the correct material is not available and the process fluid is corrosive, the use of a diaphragm seal may be necessary to protect the gauge pressure sensor from the process fluid.

Connection Size
When selecting a pressure gauge, the following mounting options should be considered:
- Direct stem mount lower connect,
- Remote wall/surface mount lower connect,
- Panel surface mount back connect,
- Panel hole U-clamp flush mount back connect,
- Panel hole front flange flush mount back connect
Select the option that best suit your application
Pressure Ranges
ASME B40.100 recommends that a gauge with a full scale pressure range of approximately twice the normal operating pressure be selected. The maximum operating pressure should not exceed 75% of the full-scale range.
Failure to select a gauge within these criteria may ultimately result in fatigue failure of the pressure sensor inside the gauge e.g Bourdon Tube
Pressure Sensor Elements
The pressure sensor elements in gauges are available in a wide variety of materials, including: brass, phosphor bronze, alloy steel, 316 stainless steel, Monel and Inconel.
The selection of the right pressure sensor for the gauge is determined by the process fluid. It is recommended that a sensor element compatible with the process fluid be selected otherwise the use of diaphragm seals is inevitable.
Type of Display
Pressure gauges are designed with analog or digital displays. Although the analog pressure gauges are the most popular, the trend in certain applications is moving towards digital displays.
The type of application will determine whether an analog or digital display pressure gauge is required. Consult ASME 40.1 and 40.7 for a detailed guide on the use of both analog dial type and digital pressure gauges
The factors discussed above are the main points you need to consider before deciding to specify and select a pressure gauge. Please consult the manufacturer of your gauge for a detailed guide.
Before consulting your manufacturer, you might want to go through ASME B 40 for a detailed guideline on pressure gauge specification and selection as this will help you with the selection process with your manufacturer or vendor.